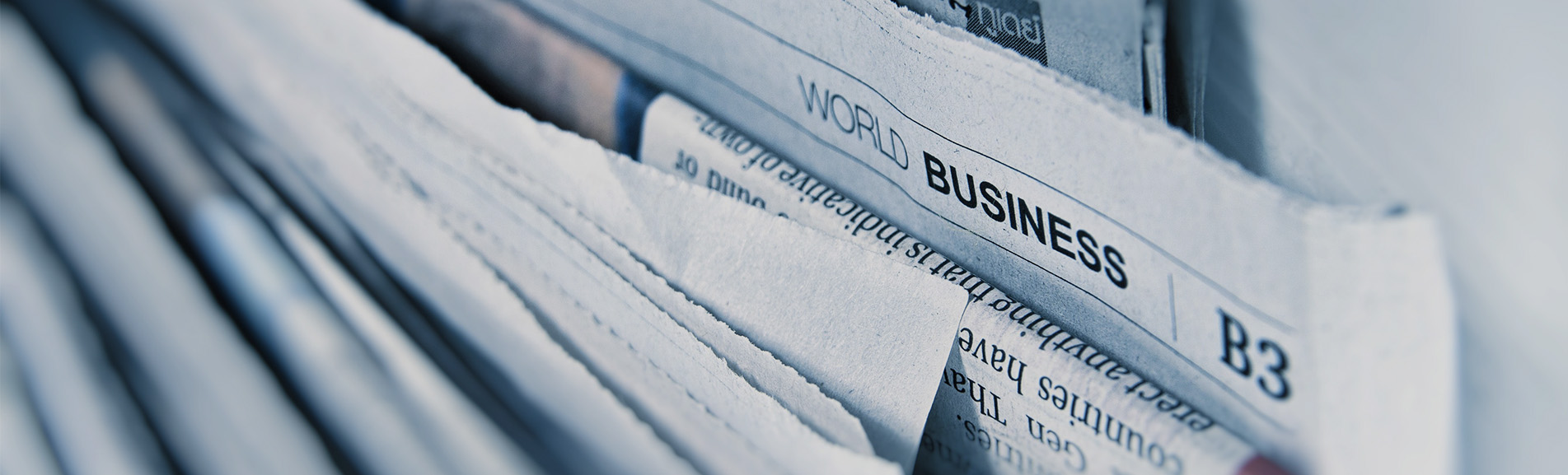
News
The principle and influencing factors of ultrasonic welding of lithium battery
The following article comes from Shun Li Chengzhang, the author Shun Li Chengzhang
As a key part of the lithium battery manufacturing process, the welding process is applied to the connection of lithium battery aluminum/copper positive and negative current collectors, pole pieces and battery packaging. Any welding joint defects will significantly affect the performance of lithium batteries. consistency. Therefore, it is necessary to understand the ultrasonic welding process.
1. Principle of ultrasonic welding In the process of ultrasonic welding, the transducer converts high-frequency electrical signals into ultrasonic vibration signals, and the high-frequency vibration is transmitted to the surface of the metal to be welded through the welding tool head, and the interface metal oxide film is under a certain pressure and ultrasonic vibration. Under the action of severe friction, the interface is clean and the metal contacts, and under the joint action of friction and ultrasonic softening, further plastic flow and diffusion are generated to gradually increase the connection area and finally form a reliable connection.
The formation of welded joints goes through two stages: the transition stage and the stabilization stage.
The transition stage is a short-term process of removing the film and oxides on the surface of the weldment, and the stable stage is the process of interdiffusion and stabilization of the interdiffusion at the interface. In the transition stage, the oxide film on the surface of the weldment is broken due to strong friction. At this time, friction is the main heat source. The increase in the temperature of the workpiece reduces the yield strength of the workpiece material, which is conducive to the breakage of the oxide film on the surface of the workpiece and the occurrence of plastic deformation. important role.
In the stable stage, the friction effect is weakened after the metal contact surface becomes smooth, and the heat accumulates at the welding interface due to plastic deformation. The heat in this process is generated by the plastic deformation process of the workpiece, and the pressure exerted by the tool head causes the interface between the atoms. The process of forming a metal connection by creating a force.
The connection interface with the workpiece is connected only under the indentation groove. The sum of the connection lengths under all the grooves of the joint connection interface is the sum of the joint connection lengths, which is called the effective connection length and is also a measure of the amount of plastic deformation.
焊接区域微观形貌
2. Research on ultrasonic metal welding process parameters The main process parameters of ultrasonic metal welding process include welding pressure, welding energy/time, tool head amplitude and tool, head tooth pattern and size, etc.
(1) The influence of pressure Welding pressure has a significant influence on the quality of welded joints, and the strength of welded joints first increases and then decreases with the increase of pressure. Welding pressure will change the sliding resistance of the welding interface. Smaller welding pressure will lead to lower sliding resistance of the interface, so that the energy generated by friction is not enough for the interface to form an effective connection; if the welding pressure is too large, the tool head is pressed too deeply, and the welding interface Metals occlude each other, which affects the relative movement of the interface, hinders the further connection of the interface metals, and leads to the deterioration of the mechanical properties of the welded joint. Therefore, suitable welding pressure parameters are decisive for the welding quality.
The influence of time The welding time directly affects the energy input during the welding process, and has a direct impact on the welding effect. If the welding time is too short and the input energy is insufficient, it is difficult to form an effective solder joint due to insufficient friction. With the increase of the welding time, the mutual friction causes the temperature to rise, the workpiece material begins to soften, and the interface oxide film in the welding area is damaged and plastically deformed. , can form a better connection; when the welding time is further prolonged, the welding head is likely to form deep traces on the surface of the workpiece, which has an adverse effect on the welding effect. bonding;
(2) Influence of amplitude In the vibration system formed by workpiece and workpiece during ultrasonic welding, the amplitude directly affects the instantaneous speed of vibration at the interface of the workpiece, and finally affects frictional heat generation and plastic deformation, which affects the welding quality.
(3) The influence of the welding head The welding head is a key component of ultrasonic metal welding. During the welding process, the welding head should grasp the workpiece to be welded under the action of pressure, so that the mechanical vibration generated by the ultrasonic welding machine can be transmitted to the interface of the workpiece to be welded. to form a solid phase connection. The different area of the welding head will lead to different distribution of welding pressure during the welding process, that is, the connection interface has different stress, which makes the friction force different during the welding process, so that the frictional heat generation during the welding process is different, resulting in different workpiece temperatures during the welding process. , which ultimately affects the quality of the joint. The tooth depth of the welding head pattern determines the difficulty of embedding the welding head pattern on the surface of the workpiece, which also directly affects the indentation depth on the surface of the workpiece, indirectly affects the temperature of the workpiece during the welding process, and affects the quality of the joint. Therefore, the shape and size of the welding head have a very critical role in the quality of the joint.
When the area of the welding head is the same, the plastic deformation degree of the rectangular welding head is stronger than that of the circular welding head; when the welding head shape is the same, the welding head with a larger area can make the plastic deformation of the welding area more intense.
When the area of the welding head is the same, the circular welding head is more likely to extrude the workpiece material under the welding head to form a deeper indentation; when the welding head has the same shape, the welding head with a small area makes the surface contact area of the workpiece larger, thus forming a Deeper indentation.
3. Welding quality monitoring
(1) Destructive test The quality of ultrasonic welding can be directly judged by detecting the tensile strength of the welding area. In the case of virtual welding and over welding, the tensile force value will be very low.
(2) Infrared test welding process parameters are different, resulting in changes in the total welding energy supplied by the welding machine to the workpiece to be welded, which will inevitably cause different frictional effects during the welding process, resulting in changes in the heat generated during the welding process, so the temperature of the workpiece during the welding process will also change. The temperature of the welding head-workpiece contact area can effectively reflect the joint strength, and the joint quality can be predicted by measuring the temperature of the workpiece during the welding process. However, the temperature in the contact zone is not as high as possible. For each material to be welded, there is a critical temperature value. When the workpiece temperature is lower than the critical temperature, the higher the temperature, the higher the joint strength; when the workpiece temperature is greater than the critical temperature, the joint strength will be higher. strength will decrease.
(3) Energy feedback With different welding parameters, the energy required for different welding effects is different, which can be judged by detecting the welding energy in the welding process.
References
1. Kim T H , Yum J , Hu S J , et al. Processrobustness of single lap ultrasonic welding of thin, dissimilar materials[J]. CIRP Annals - Manufacturing Technology, 2011, 60(1): 17-20.2, Bakavos D, Prangnell P B. Mechanisms of joint and microstructure formation in high power ultrasonic spot welding 6111 aluminiumautomotive sheet[J]. Materials Science and Engineering: A,2010,527(23):6320-63343, Li Dong, Zhao Yangyang, Zhang Yansong. Influence of size on plastic deformation of copper/aluminum ultrasonic welded joints[J]. Thermal processing technology (9):157-159.4, Li Dong. Optimization method of ultrasonic welding process for metal pole pieces in the manufacture of laminated lithium batteries [D]. Shanghai Jiaotong University, 20135, Xiao Zhongyang. Research on the technology and mechanism of ultrasonic bonding of strip metal foil[D].