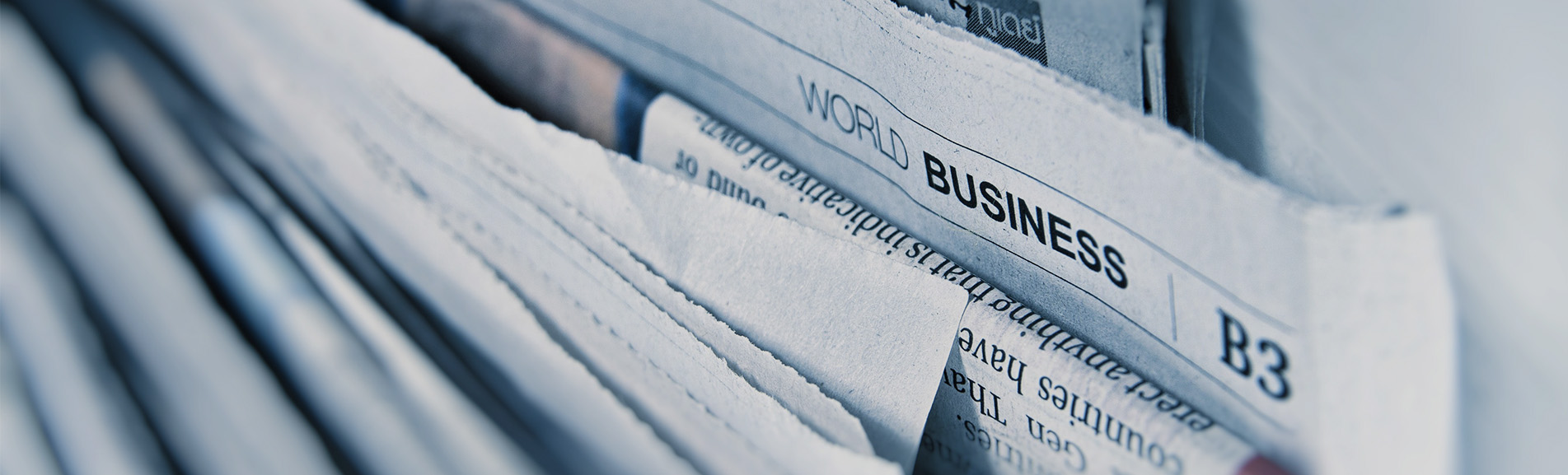
News
Modular design reduces the cost of AGV
"International Industrial Vehicle Magazine" published an article on the design concept of AGV in the September issue of the magazine, from the modularization of design, to reduce the design cost of AGV and the cost of processing and manufacturing. More and more AGV companies are also looking for more versatile AGV designs. The content of the article is as follows.
Andreas Panik and Christian Ebner are the two Stuttgart designers behind Panik Ebner Design. They have designed everything from trains and off-road vehicles for exhibitions and graphic displays
PanikEbner has been working on design projects in the field of automated guided vehicles (AGV) and machine building since 2018. During this period, the company has witnessed the rapid development of the Internet of Things (Industry 4.0).
This leads to an increasing demand in the field of automation and connectivity in industrial processes. These requirements include centralization of process control, task and demand management of machines and vehicles, independent battery management of vehicles, control and display of operating status.
Andreas Panik said: "Working with customers, we have observed a strong demand for AGVs with very individual requirements in terms of size, control and drive, keeping the development team in the technical department constantly busy." For the design challenge, we took this Opportunity to condense some ideas into design concepts that can be of some help to the industry.
Modular and flexible
Modularity is the concept of AGV design. The motivation is to provide flexible products to small and medium manufacturers. Ideally, this should be able to map out a certain number of material handling and industrial production scenarios without requiring the development team to do too much onerous redesign work for each new customer.
"Automation and connectivity of industrial production and cargo management processes requires comprehensive investments in the concept and implementation of logistics and infrastructure," he says. Or for converting large parts of existing transport fleets.
We understand that this is a high barrier to entry for many small companies using AGVs.
Cost reduction
Considering the idea of how to rely on modularity to reduce the cost of design and production, their design team decided to start with a pallet truck as the basic module. The next step is to provide platform trucks and light forklifts as composable functional modules.
To reduce investment costs, the powertrain, steerable chassis and main control processor are configured in the base module, as well as a powerful battery. The wheels on the forks are steerable, but have no power on their own. The two functional modules have complementary control processors, batteries to support their own functions, and unpowered chassis.
Coupling and decoupling basic and functional modules can be done according to upcoming loading and transport tasks.
Scanning for safety
Operational issues are also a core aspect of the design. The 360° environmental scanning area on the fork head has no blind spots, and has distance sensors, providing good safety features.
The state of the vehicle in motion and the state indication are important in this context. Therefore, many LED displays work in all directions.
Panik concluded: "For the exterior of the vehicle, we deliberately chose a very robust and rational design that should inspire confidence and allow the structure of the vehicle to be designed in a way that is understandable at first glance.
This news comes from - China Forklift Tribe