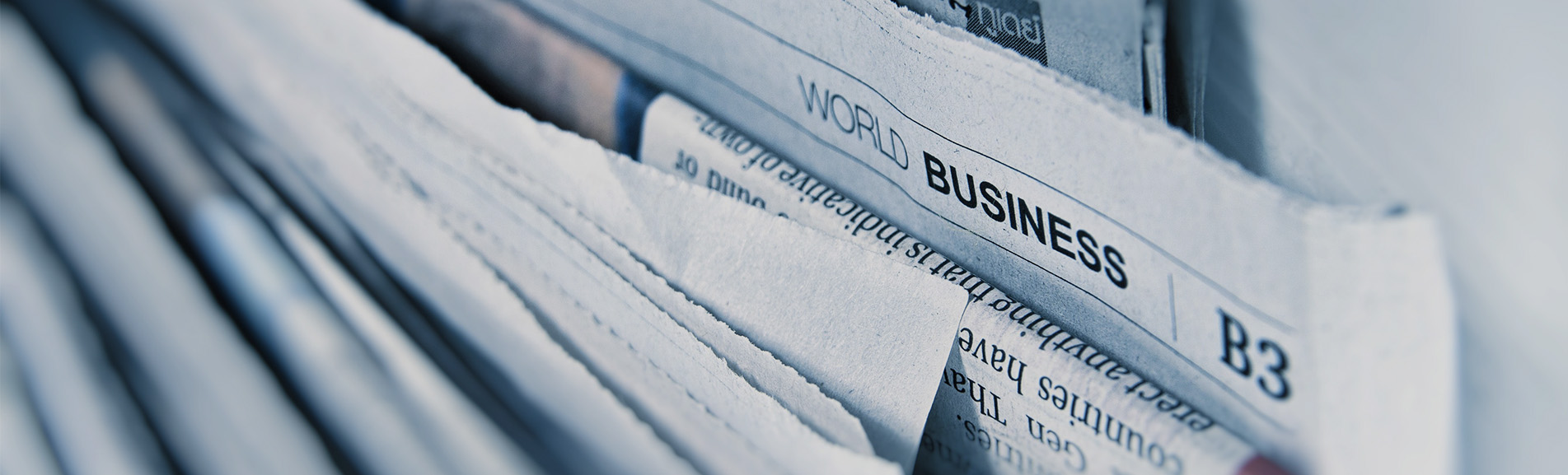
新闻资讯
Discussion on Cell Cycle Failure Analysis Process
The following article comes from Battery Ark, the author is chasing the wind
The ternary power battery used has a life guarantee of 8 years or 150,000 kilometers or even higher. Assuming that a full charge can run 400 kilometers once, the battery pack life needs to be 400-500 times. If it is converted to the battery, consider During the use of the whole vehicle, the temperature difference and the consistency level of the cells throughout the year, the main engine factory requires the cycle life of the single cell, the normal temperature needs to reach the level of more than 1500 to 2000 times, and the high temperature also needs to reach the level of more than 800 to 1000 times. Level.
If the cycle life of the battery cell is actually measured and there is a large gap with the target, then we generally define this situation as cycle failure, and we need to conduct failure analysis to find the cause of the failure, and provide targeted solutions to reach customers. life expectancy requirements.
For engineers who develop power cells, cycle failure is a problem we often encounter in the development stage, which can be roughly divided into diving type and linear Fading type. The schematic diagram is as follows:
Since the failed cell cannot be copied, if you dismantle it immediately after you get it, you may miss some important non-destructive analysis, which is a pity; , CP, ICP, buckling, symmetrical battery, etc.), the final various test results are difficult to draw effective conclusions and cannot support our next improvement. In the process of developing square cells, the author combined with some experience in the analysis of cyclic failure problems, and made the following sharing for the analysis ideas:
The analysis idea is mainly carried out according to the PDCA rule, as shown in the following figure: (You can also choose 5Why, 3W2H, 8D, etc., as long as you can solve the problem, the focus is on flexible use)
The first step in analysis is to think about:
What is the real problem?
What are the deeper problems with loop diving?
How to dig?
…………
To answer these questions, data investigation and collection are essential, and we can start from the following aspects:
The first step in analysis is to think about:
What is the real problem?
What are the deeper problems with loop diving?
How to dig?
…………
To answer these questions, data investigation and collection are essential, and we can start from the following aspects:
排查工序 | 名称 | 详细信息 |
来料检测 | 阴极 | 粒径分布,克容量,首效率,杂质含量,残碱量,磁性杂质等 |
阳极 | 粒径分布,克容量,首效率,杂质含量,振实密度,石墨化度等 | |
隔膜 | 孔隙度,透气率,陶瓷涂重,浸润等 | |
电解液 | 水含量,电导率,存放时间,杂质含量等 | |
搅拌 | 浆料配方,固含量,粘度,流变,剪切,颗粒度等 | |
涂布 | 涂布重量分布,留样观察,不良统计 | |
冷压 | 粘结力,压密数据,厚度反弹等 | |
热压 | 热压参数,Hip-pot参数,不良统计 | |
注液 | 环境参数,JR水含量,注液系数,静置时间 | |
化成 | 化成流程,化成曲线,同批次拆解界面 |
Check the same chemical system, analyze the design of the same chemical system, and verify whether there are any problems on the small soft pack. If conditions permit, you can also check whether similar problems have occurred in other projects;
Through these preliminary positioning analysis, we have basically analyzed the external performance of cyclically failed cells (abnormal growth of DCR, too fast growth of expansion force, fluctuation of incoming batches, insufficient liquid injection coefficient, gas production due to cell failure, etc.) Make an estimate of possible failure causes, so that in the next step of the battery disassembly process, we can purposefully observe the relevant details and retain samples.
The second step, what to see and what to keep when disassembling the battery
Before disassembling the battery, think about what state we want to disassemble. If it is to observe the interface, it is best to be fully charged. If it is purely for the follow-up sample analysis and various battery production, it is better to be fully discharged. After the cell is disassembled, the interface conditions, the thickness of the core at different positions, the amount of free electrolyte, the lithium deposition of the anode, the thickness of the pole piece, etc., should be photographed and recorded completely. According to our follow-up experimental plan, for the electrode Sheets, diaphragms and free electrolyte (if any) are sealed separately for reserve samples.
The third step is to design and verify the experimental verification conjecture according to the dismantling results
It is very important for failure analysis to achieve this step. At this time, a small-scale speculation has been made based on the data of investigation and disassembly. At this time, it is necessary to list the possible failure causes (simple FTA failure analysis tree) according to the actual situation. You can use Xmind to quickly and effectively help analyze, design corresponding experiments, and do targeted tests. An example is as follows:
The fourth step is to formulate improvement measures and verify the process. This step is to propose corresponding improvement plans, design new cells, and test and evaluate the results according to the failure reasons obtained from the verification. If the final test results show that the cell cycle has been improved and the target has been achieved, then the failure analysis can be completed; if not, the analysis and improvement must be continued according to the PDCA rule.
To sum up, the work of cell failure analysis requires a clearer logical thinking ability, as well as a wealth of R&D and production experience. For small partners who are just starting to develop batteries, failure analysis is a good way to exercise and improve their thinking ability.